Plastic extrusion services for bespoke industrial applications
Plastic extrusion services for bespoke industrial applications
Blog Article
A Comprehensive Guide to the Refine and Benefits of Plastic Extrusion
In the large world of production, plastic extrusion becomes a essential and highly efficient process. Translating raw plastic into constant accounts, it accommodates a wide variety of sectors with its amazing adaptability. This guide aims to clarify the intricate steps associated with this method, the sorts of plastic suitable for extrusion, and the game-changing advantages it brings to the market. The occurring conversation guarantees to unravel the real-world impacts of this transformative process.
Comprehending the Essentials of Plastic Extrusion
While it may appear complicated at first glance, the process of plastic extrusion is essentially basic - plastic extrusion. It is a high-volume production strategy in which raw plastic is melted and shaped into a continual profile. The procedure starts with the feeding of plastic material, in the form of granules, pellets, or powders, into a heated barrel. The plastic is then thawed making use of a mix of heat and shear, used by a turning screw. When the molten plastic reaches completion of the barrel, it is compelled via a tiny opening referred to as a die, forming it right into a preferred type. The shaped plastic is after that cooled down, strengthened, and reduced right into wanted sizes, finishing the procedure.
The Technical Process of Plastic Extrusion Explained
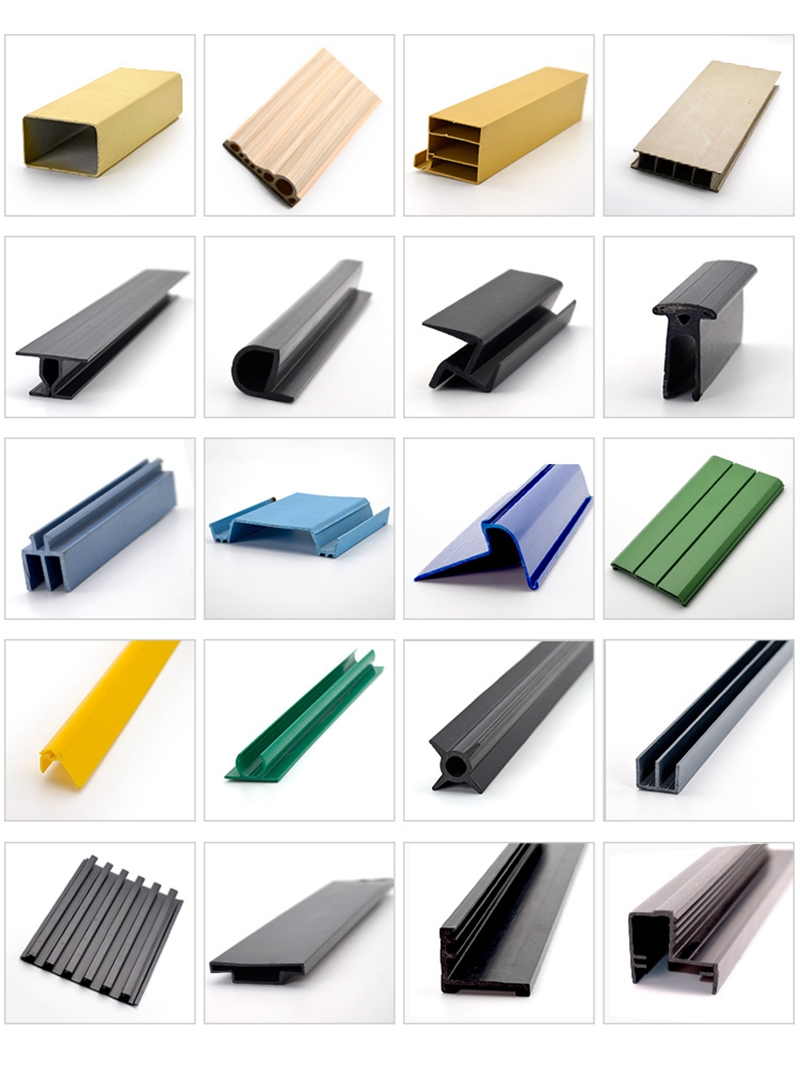
Kinds Of Plastic Suitable for Extrusion
The choice of the right kind of plastic is an important facet of the extrusion procedure. Various plastics provide unique buildings, making them a lot more suited to certain applications. Polyethylene, for instance, is frequently made use of because of its inexpensive and very easy formability. It offers superb resistance to chemicals and dampness, making it excellent for products like tubes and containers. Similarly, polypropylene is another popular option because of its high melting point and resistance to exhaustion. For more robust applications, polystyrene and PVC (polyvinyl chloride) are typically chosen for their stamina and toughness. Although these are usual alternatives, the option eventually relies on the details needs of the item being created. Recognizing these plastic types can significantly enhance the extrusion procedure.
Contrasting Plastic Extrusion to Other Plastic Forming Approaches
Understanding the kinds of plastic suitable for extrusion leads the way for a more comprehensive conversation on how plastic extrusion compares to various other plastic forming approaches. These include shot molding, blow molding, and thermoforming. Each approach has its unique uses and benefits. Shot molding, for example, is superb for producing intricate parts, while strike molding is ideal for hollow things like bottles. Thermoforming excels at developing large or shallow components. However, plastic extrusion is unrivaled when it pertains to developing continuous accounts, such as seals, gaskets, and pipes. It additionally enables a regular cross-section along the size of the item. Thus, the option of approach mostly depends upon the end-product requirements and specs.
Secret Advantages of Plastic Extrusion in Manufacturing
In the world of production, plastic extrusion offers many considerable benefits. One noteworthy advantage is the cost-effectiveness of the process, that makes it an economically appealing production technique. In addition, this strategy gives remarkable item versatility and enhanced production rate, thereby increasing overall manufacturing effectiveness.
Cost-Effective Manufacturing Approach
Plastic extrusion jumps to the center as an affordable manufacturing approach in production. Additionally, plastic extrusion needs less energy than traditional manufacturing approaches, contributing to lower operational costs. In general, the financial benefits make plastic extrusion a highly attractive option in the manufacturing sector.
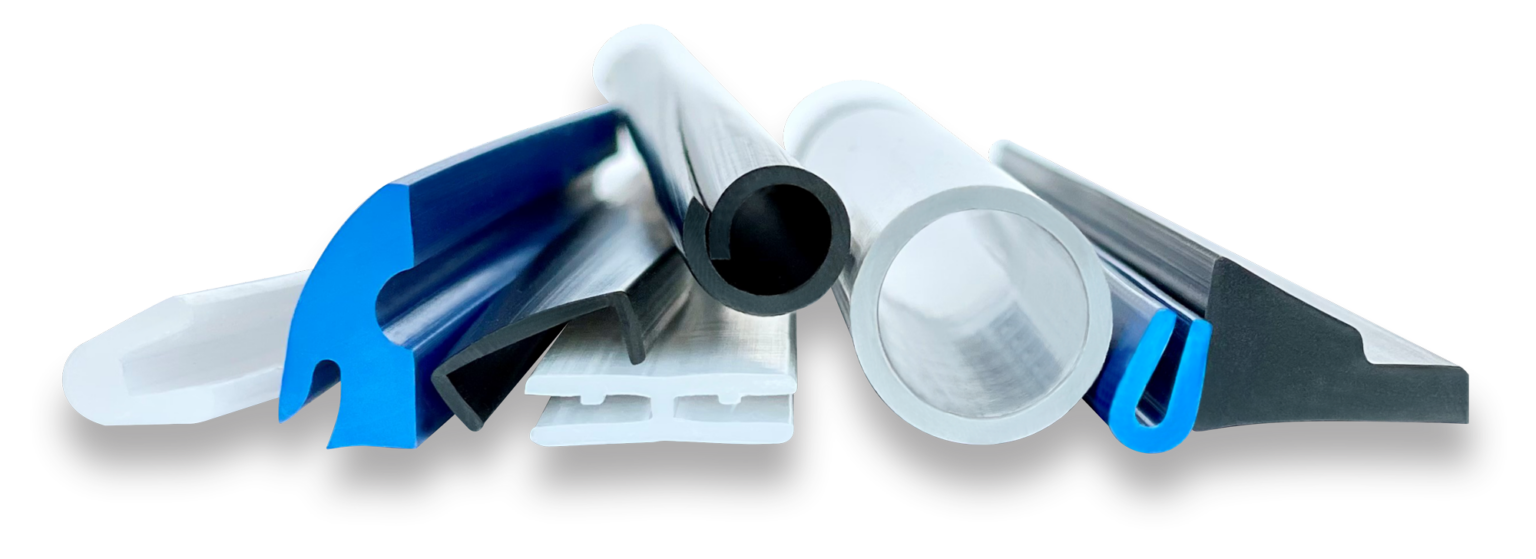
Superior Product Flexibility
Past the cost-effectiveness of plastic extrusion, another significant benefit in producing depend on its remarkable product versatility. This process permits the development of a vast variety of products with differing sizes, designs, and forms, from simple plastic sheets to detailed profiles. The versatility is credited to the extrusion die, which can be tailored to generate the desired product layout. This makes plastic extrusion an excellent service for sectors that need personalized plastic components, such as automobile, building, and packaging. The capacity to generate varied products is not only valuable in meeting certain market needs however additionally in making it possible for producers to check out brand-new item lines with very little resources investment. Basically, plastic extrusion's visite site product adaptability cultivates development while enhancing operational efficiency.
Boosted Manufacturing Speed
A considerable advantage of plastic extrusion exists in its boosted production rate. Couple of various other manufacturing procedures can match the rate of plastic extrusion. Furthermore, the ability to maintain consistent high-speed production without compromising product top quality establishes plastic extrusion apart from other approaches.
Real-world Applications and Impacts of Plastic Extrusion
In the realm of manufacturing, the technique of plastic navigate to these guys extrusion holds extensive relevance. The financial benefit of plastic extrusion, primarily its cost-effective and high-volume outcome, has reinvented production. The industry is persistently striving for technologies in recyclable and naturally degradable materials, suggesting a future where the advantages of plastic extrusion can be retained without endangering ecological sustainability.
Verdict
In final thought, plastic extrusion is a very efficient and efficient method of changing basic materials into varied products. It offers numerous benefits over various other plastic developing techniques, consisting of cost-effectiveness, high outcome, marginal waste, and style adaptability. Its effect is greatly felt in numerous sectors such as building, automotive, and durable goods, making it a critical process in today's production landscape.
Digging much deeper right into the technological process of plastic extrusion, it starts with the selection of the proper plastic material. Once cooled, the plastic is cut into the required lengths or injury onto reels if the product is a plastic movie or sheet - plastic extrusion. Comparing Plastic Extrusion to Other Plastic Forming Techniques
Understanding the kinds of plastic ideal for extrusion leads the way for a wider discussion on just how plastic extrusion piles up against various other plastic developing techniques. Couple of other manufacturing visit here processes can match the speed of plastic extrusion.
Report this page